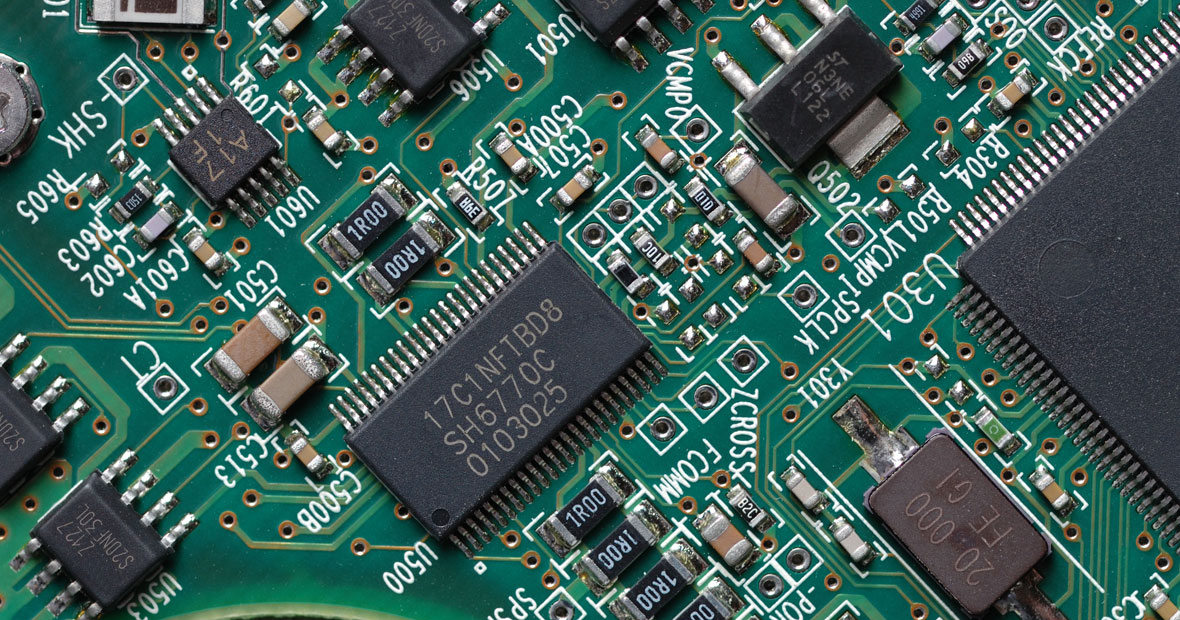
In the realm of electronics manufacturing, the demand for materials that strike a balance between durability, performance, and weight has never been higher. Aluminum Printed Circuit Boards (PCBs) have emerged as a frontrunner in this domain, offering an enticing blend of lightweight properties coupled with robust resilience. Beyond just these attributes, Aluminum PCBs present a suite of benefits that make them the go-to choice for many modern electronic applications. This article delves into the advantages of Aluminum PCB, unraveling why they are increasingly becoming a staple in the electronics industry.
Deciphering Aluminum PCBs and their Unique Features
Aluminum printed circuit boards (PCBs) have become increasingly popular in various industries due to their unique features and benefits. These PCBs are constructed using a base material of aluminum instead of the traditional FR4 material. This results in a number of advantages that make aluminum PCBs a preferred choice for many applications. One of the key features of aluminum PCBs is their high thermal conductivity. This allows for better heat dissipation, making them ideal for applications that generate a significant amount of heat. Aluminum PCBs also offer excellent electrical performance, high rigidity, and lightweight construction, which further contribute to their appeal.
High Thermal Conductivity: An Important Advantage of Aluminum PCBs
Role of Thermal Conductivity in PCB Performance
Thermal conductivity plays a crucial role in determining the performance and reliability of printed circuit boards. It refers to the ability of a material to conduct heat. In PCBs, efficient heat dissipation is vital to prevent overheating, which can lead to component failure and reduced lifespan. Aluminum PCBs excel in this aspect due to their high thermal conductivity. The aluminum base material allows for better heat transfer, ensuring that heat generated by components is effectively dissipated. This results in improved performance and increased reliability, particularly in applications where temperature management is critical.
Comparing Thermal Conductivity: Aluminum vs Copper and Steel
When it comes to thermal conductivity, aluminum PCBs outperform copper and steel. While copper is also known for its high thermal conductivity, aluminum offers a comparable or even better performance. Aluminum is approximately four times lighter than copper, making it an excellent choice for applications that require lightweight and compact designs. Steel, on the other hand, has much lower thermal conductivity compared to aluminum and copper. This makes aluminum PCBs a more efficient option in terms of heat dissipation. The lightweight nature of aluminum also reduces the overall weight of the PCB, making it more suitable for mobile and portable devices.
Applications Benefitting from High Thermal Conductivity
The high thermal conductivity of aluminum PCBs makes them well-suited for a wide range of applications. Some of the industries where aluminum PCBs are commonly used include:
- LED lighting: Aluminum PCBs are widely used in LED lighting applications due to their ability to efficiently dissipate heat generated by the LED components, resulting in improved performance and increased lifespan.
- Power electronics: Applications such as power supplies, motor drives, and inverters benefit greatly from the high thermal conductivity of aluminum PCBs. These applications often generate substantial amounts of heat that need to be efficiently managed.
- Automotive industry: The automotive industry relies on aluminum PCBs for various electronic components, including engine control units (ECUs), lighting systems, and infotainment systems. The high thermal conductivity of aluminum helps ensure the reliability and longevity of these components in demanding automotive environments.
Compact and Lightweight: Reasons Why Aluminum PCBs are Preferred
The compact and lightweight nature of aluminum PCBs is another significant advantage that contributes to their popularity. Aluminum PCBs offer a much higher strength-to-weight ratio compared to traditional FR4 PCBs. This means that they can handle increased mechanical stress while maintaining a lightweight construction. The reduced weight is particularly beneficial for applications where weight is a critical factor, such as aerospace and portable electronic devices. The compact size of aluminum PCBs also allows for more efficient use of space in electronic designs. With the continuous miniaturization of electronic components, the compactness of aluminum PCBs becomes even more valuable, enabling manufacturers to create smaller, more streamlined products.
Enhancing Durability and Performance with Aluminum PCBs
In addition to their thermal conductivity and lightweight construction, aluminum PCBs offer enhanced durability and performance. The rigidity of aluminum PCBs makes them less susceptible to mechanical stress and vibration. This helps reduce the risk of component failure, ensuring the reliability of the PCB in various operating conditions. Furthermore, aluminum PCBs have excellent thermal stability, allowing them to withstand rapid temperature changes without delamination or warping. This makes them suitable for applications that undergo extreme temperature variations, such as automotive electronics or industrial control systems.
Economic and Environmental Benefits of Aluminum PCBs
Reduced Manufacturing Costs with Aluminum PCBs
Manufacturers can benefit from the use of aluminum PCBs in terms of reduced manufacturing costs. The simplified manufacturing process, compared to traditional PCBs, helps save time and resources. The use of aluminum as a base material eliminates the need for additional thermal management solutions, reducing both material and assembly costs. Additionally, the lightweight nature of aluminum PCBs translates into lower transportation costs. The reduced weight allows for more efficient shipping and handling, leading to cost savings throughout the supply chain.
Energy Efficiency Gained from Using Aluminum PCBs
The high thermal conductivity of aluminum PCBs contributes to energy efficiency in electronic systems. By efficiently dissipating heat, these PCBs help maintain optimal operating temperatures, reducing the energy required for cooling mechanisms. This results in improved energy efficiency and lower power consumption, which is particularly valuable in applications where energy efficiency is a priority, such as solar power systems or battery-operated devices.
Recyclability: A Key Environmental Benefit of Aluminum PCBs
Aluminum PCBs are highly recyclable, contributing to the sustainability of electronic manufacturing processes. Aluminum is a valuable material that can be easily recovered and reused, reducing the need for virgin materials. The recycling of aluminum PCBs helps conserve natural resources and minimize waste, making it an environmentally friendly choice. In conclusion, aluminum PCBs offer numerous benefits that make them an attractive option for various industries. Their high thermal conductivity, lightweight construction, durability, and economic and environmental advantages make them well-suited for applications ranging from LED lighting to automotive electronics.
By choosing aluminum PCBs, manufacturers can enhance the performance, reliability, and sustainability of their electronic products.